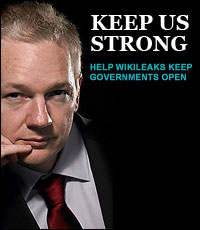
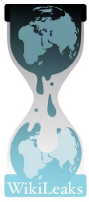
Currently released so far... 64621 / 251,287
Articles
Brazil
Sri Lanka
United Kingdom
Sweden
00. Editorial
United States
Latin America
Egypt
Jordan
Yemen
Thailand
Browse latest releases
2010/12/01
2010/12/02
2010/12/03
2010/12/04
2010/12/05
2010/12/06
2010/12/07
2010/12/08
2010/12/09
2010/12/10
2010/12/11
2010/12/12
2010/12/13
2010/12/14
2010/12/15
2010/12/16
2010/12/17
2010/12/18
2010/12/19
2010/12/20
2010/12/21
2010/12/22
2010/12/23
2010/12/25
2010/12/26
2010/12/27
2010/12/28
2010/12/29
2010/12/30
2011/01/01
2011/01/02
2011/01/04
2011/01/05
2011/01/07
2011/01/09
2011/01/11
2011/01/12
2011/01/13
2011/01/14
2011/01/15
2011/01/16
2011/01/17
2011/01/18
2011/01/19
2011/01/20
2011/01/21
2011/01/22
2011/01/23
2011/01/24
2011/01/25
2011/01/26
2011/01/27
2011/01/28
2011/01/29
2011/01/30
2011/01/31
2011/02/01
2011/02/02
2011/02/03
2011/02/04
2011/02/05
2011/02/06
2011/02/07
2011/02/08
2011/02/09
2011/02/10
2011/02/11
2011/02/12
2011/02/13
2011/02/14
2011/02/15
2011/02/16
2011/02/17
2011/02/18
2011/02/19
2011/02/20
2011/02/21
2011/02/22
2011/02/23
2011/02/24
2011/02/25
2011/02/26
2011/02/27
2011/02/28
2011/03/01
2011/03/02
2011/03/03
2011/03/04
2011/03/05
2011/03/06
2011/03/07
2011/03/08
2011/03/09
2011/03/10
2011/03/11
2011/03/13
2011/03/14
2011/03/15
2011/03/16
2011/03/17
2011/03/18
2011/03/19
2011/03/20
2011/03/21
2011/03/22
2011/03/23
2011/03/24
2011/03/25
2011/03/26
2011/03/27
2011/03/28
2011/03/29
2011/03/30
2011/03/31
2011/04/01
2011/04/02
2011/04/03
2011/04/04
2011/04/05
2011/04/06
2011/04/07
2011/04/08
2011/04/09
2011/04/10
2011/04/11
2011/04/12
2011/04/13
2011/04/14
2011/04/15
2011/04/16
2011/04/17
2011/04/18
2011/04/19
2011/04/20
2011/04/21
2011/04/22
2011/04/23
2011/04/24
2011/04/25
2011/04/26
2011/04/27
2011/04/28
2011/04/29
2011/04/30
2011/05/01
2011/05/02
2011/05/03
2011/05/04
2011/05/05
2011/05/06
2011/05/07
2011/05/08
2011/05/09
2011/05/10
2011/05/11
2011/05/12
2011/05/13
2011/05/14
2011/05/15
2011/05/16
2011/05/17
2011/05/18
2011/05/19
2011/05/20
2011/05/21
2011/05/22
2011/05/23
2011/05/24
2011/05/25
2011/05/26
2011/05/27
2011/05/28
2011/05/29
2011/05/30
2011/05/31
2011/06/01
2011/06/02
2011/06/03
2011/06/04
2011/06/05
2011/06/06
2011/06/07
2011/06/08
2011/06/09
2011/06/10
2011/06/11
2011/06/12
2011/06/13
2011/06/14
2011/06/15
2011/06/16
2011/06/17
2011/06/18
2011/06/19
2011/06/20
2011/06/21
2011/06/22
2011/06/23
2011/06/24
2011/06/25
2011/06/26
2011/06/27
2011/06/28
2011/06/29
2011/06/30
2011/07/01
2011/07/02
2011/07/04
2011/07/05
2011/07/06
2011/07/07
2011/07/08
2011/07/10
2011/07/11
2011/07/12
2011/07/13
2011/07/14
2011/07/15
2011/07/16
2011/07/17
2011/07/18
2011/07/19
2011/07/20
2011/07/21
2011/07/22
2011/07/23
2011/07/25
2011/07/27
2011/07/28
2011/07/29
2011/07/31
2011/08/01
2011/08/02
2011/08/03
2011/08/05
2011/08/06
2011/08/07
2011/08/08
2011/08/09
2011/08/10
2011/08/11
2011/08/12
2011/08/13
2011/08/15
2011/08/16
2011/08/17
2011/08/18
2011/08/19
2011/08/21
2011/08/22
2011/08/23
2011/08/24
Browse by creation date
Browse by origin
Embassy Athens
Embassy Asuncion
Embassy Astana
Embassy Asmara
Embassy Ashgabat
Embassy Apia
Embassy Antananarivo
Embassy Ankara
Embassy Amman
Embassy Algiers
Embassy Addis Ababa
Embassy Accra
Embassy Abuja
Embassy Abu Dhabi
Embassy Abidjan
Consulate Auckland
Consulate Amsterdam
Consulate Alexandria
Consulate Adana
American Institute Taiwan, Taipei
Embasy Bonn
Embassy Bujumbura
Embassy Buenos Aires
Embassy Budapest
Embassy Bucharest
Embassy Brussels
Embassy Bridgetown
Embassy Brazzaville
Embassy Bratislava
Embassy Brasilia
Embassy Bogota
Embassy Bishkek
Embassy Bern
Embassy Berlin
Embassy Belmopan
Embassy Belgrade
Embassy Beirut
Embassy Beijing
Embassy Banjul
Embassy Bangui
Embassy Bangkok
Embassy Bandar Seri Begawan
Embassy Bamako
Embassy Baku
Embassy Baghdad
Consulate Belfast
Consulate Barcelona
Embassy Cotonou
Embassy Copenhagen
Embassy Conakry
Embassy Colombo
Embassy Chisinau
Embassy Caracas
Embassy Canberra
Embassy Cairo
Consulate Curacao
Consulate Ciudad Juarez
Consulate Chiang Mai
Consulate Chennai
Consulate Chengdu
Consulate Casablanca
Consulate Cape Town
Consulate Calgary
Embassy Dushanbe
Embassy Dublin
Embassy Doha
Embassy Djibouti
Embassy Dili
Embassy Dhaka
Embassy Dar Es Salaam
Embassy Damascus
Embassy Dakar
DIR FSINFATC
Consulate Dusseldorf
Consulate Durban
Consulate Dubai
Consulate Dhahran
Embassy Guatemala
Embassy Grenada
Embassy Georgetown
Embassy Gaborone
Consulate Guayaquil
Consulate Guangzhou
Consulate Guadalajara
Embassy Helsinki
Embassy Harare
Embassy Hanoi
Consulate Hong Kong
Consulate Ho Chi Minh City
Consulate Hermosillo
Consulate Hamilton
Consulate Hamburg
Consulate Halifax
Embassy Kyiv
Embassy Kuwait
Embassy Kuala Lumpur
Embassy Kolonia
Embassy Kinshasa
Embassy Kingston
Embassy Kigali
Embassy Khartoum
Embassy Kathmandu
Embassy Kampala
Embassy Kabul
Consulate Krakow
Consulate Kolkata
Consulate Karachi
Embassy Luxembourg
Embassy Lusaka
Embassy Luanda
Embassy London
Embassy Lome
Embassy Ljubljana
Embassy Lisbon
Embassy Lima
Embassy Lilongwe
Embassy Libreville
Embassy La Paz
Consulate Leipzig
Consulate Lahore
Consulate Lagos
Mission USOSCE
Mission USNATO
Mission UNESCO
Mission Geneva
Embassy Muscat
Embassy Moscow
Embassy Montevideo
Embassy Monrovia
Embassy Mogadishu
Embassy Minsk
Embassy Mexico
Embassy Mbabane
Embassy Maseru
Embassy Maputo
Embassy Manila
Embassy Manama
Embassy Managua
Embassy Malabo
Embassy Madrid
Consulate Munich
Consulate Mumbai
Consulate Montreal
Consulate Monterrey
Consulate Milan
Consulate Merida
Consulate Melbourne
Consulate Matamoros
Consulate Marseille
Embassy Nouakchott
Embassy Nicosia
Embassy Niamey
Embassy New Delhi
Embassy Ndjamena
Embassy Nassau
Embassy Nairobi
Consulate Nuevo Laredo
Consulate Naples
Consulate Naha
Consulate Nagoya
Embassy Pristina
Embassy Pretoria
Embassy Praia
Embassy Prague
Embassy Port Of Spain
Embassy Port Moresby
Embassy Port Louis
Embassy Port Au Prince
Embassy Podgorica
Embassy Phnom Penh
Embassy Paris
Embassy Paramaribo
Embassy Panama
Consulate Peshawar
REO Mosul
REO Kirkuk
REO Hillah
REO Basrah
Embassy Rome
Embassy Riyadh
Embassy Riga
Embassy Reykjavik
Embassy Rangoon
Embassy Rabat
Consulate Rio De Janeiro
Consulate Recife
Secretary of State
Embassy Suva
Embassy Stockholm
Embassy Sofia
Embassy Skopje
Embassy Singapore
Embassy Seoul
Embassy Sarajevo
Embassy Santo Domingo
Embassy Santiago
Embassy Sanaa
Embassy San Salvador
Embassy San Jose
Consulate Surabaya
Consulate Strasbourg
Consulate St Petersburg
Consulate Shenyang
Consulate Shanghai
Consulate Sapporo
Consulate Sao Paulo
Embassy Tunis
Embassy Tripoli
Embassy Tokyo
Embassy Tirana
Embassy The Hague
Embassy Tel Aviv
Embassy Tehran
Embassy Tegucigalpa
Embassy Tbilisi
Embassy Tashkent
Embassy Tallinn
Consulate Toronto
Consulate Tijuana
Consulate Thessaloniki
USUN New York
USMISSION USTR GENEVA
USEU Brussels
US Office Almaty
US Mission Geneva
US Mission CD Geneva
US Interests Section Havana
US Delegation, Secretary
US Delegation FEST TWO
UNVIE
UN Rome
Embassy Ulaanbaatar
Embassy Vilnius
Embassy Vientiane
Embassy Vienna
Embassy Vatican
Embassy Valletta
Consulate Vladivostok
Consulate Vancouver
Browse by tag
AMGT
ASEC
AEMR
AR
APECO
AU
AORC
AS
ADANA
AJ
AF
AFIN
AMED
AM
ABLD
AFFAIRS
AMB
APER
ACOA
AG
AA
AE
ABUD
ARABL
AO
AND
ASECKFRDCVISKIRFPHUMSMIGEG
AID
AL
ASCH
AADP
AORD
ADM
AINF
AINT
ASEAN
AORG
AY
ABT
ARF
AGOA
AVIAN
APEC
ANET
AGIT
ASUP
ATRN
ASECVE
ALOW
AODE
AGUILAR
AN
ADB
ASIG
ADPM
AT
ACABQ
AGR
ASPA
AFSN
AZ
AC
ALZUGUREN
ANGEL
AIAG
AFSI
ASCE
ABMC
ANTONIO
AIDS
ASEX
ADIP
ALJAZEERA
AFGHANISTAN
ASECARP
AROC
ASE
ABDALLAH
ADCO
AMGMT
AMCHAMS
AGAO
ACOTA
ANARCHISTS
AMEDCASCKFLO
AK
ARSO
ARABBL
ASO
ANTITERRORISM
AGRICULTURE
AFINM
AOCR
ARR
AFPK
ASSEMBLY
AORCYM
AINR
ACKM
AGMT
AEC
APRC
AIN
AFPREL
ASFC
ASECTH
AFSA
ANTXON
AFAF
AFARI
AX
AMER
ASECAF
ASECAFIN
AFZAL
APCS
AGUIRRE
AIT
ARCH
AEMRASECCASCKFLOMARRPRELPINRAMGTJMXL
AOPC
AMEX
ARM
ALI
AQ
ATFN
AMBASSADOR
AORCD
AVIATION
ARAS
AINFCY
ACBAQ
AOPR
AREP
ALEXANDER
AMTC
AOIC
ABLDG
ASEK
AER
ALOUNI
AMCT
AVERY
APR
AMAT
AEMRS
AFU
AMG
ATPDEA
ALL
AORL
ACS
AECL
AUC
ACAO
BA
BR
BB
BG
BEXP
BY
BRUSSELS
BU
BD
BTIO
BK
BL
BO
BE
BMGT
BM
BN
BWC
BBSR
BTT
BX
BC
BH
BEN
BUSH
BF
BHUM
BILAT
BT
BTC
BMENA
BBG
BOND
BAGHDAD
BAIO
BP
BRPA
BURNS
BUT
BGMT
BCW
BOEHNER
BOL
BASHAR
BOU
BIDEN
BTRA
BFIN
BOIKO
BZ
BERARDUCCI
BOUCHAIB
BEXPC
BTIU
CPAS
CA
CASC
CS
CBW
CIDA
CO
CODEL
CI
CROS
CU
CH
CWC
CMGT
CVIS
CDG
CTR
CG
CF
CD
CHIEF
CJAN
CBSA
CE
CY
CB
CW
CM
CDC
COUNTRY
CLEARANCE
CHR
CT
COE
CV
COUNTER
CN
CPUOS
CTERR
CVR
CVPR
COUNTRYCLEARANCE
CLOK
CONS
CITES
COM
CONTROLS
CAN
CACS
CR
CACM
CVISCMGTCASCKOCIASECPHUMSMIGKIRF
COMMERCE
CAMBODIA
CZ
CJ
CFIS
CASCC
COUNTERTERRORISM
CAS
CONDOLEEZZA
CLINTON
CTBT
CEN
CRISTINA
CFED
CARC
CTM
CARICOM
CSW
CICTE
CJUS
CYPRUS
CNARC
CBE
CMGMT
CARSON
CWCM
CIVS
CENTCOM
COPUOS
CAPC
CGEN
CKGR
CITEL
CQ
CITT
CIC
CARIB
CVIC
CAFTA
CVISU
CHRISTOPHER
CDB
CEDAW
CNC
COMMAND
CENTER
COL
CAJC
CUIS
CONSULAR
CLMT
CBC
CIA
CIS
CEUDA
CHINA
CAC
CL
DR
DJ
DEMOCRATIC
DEMARCHE
DA
DOMESTIC
DISENGAGEMENT
DRL
DB
DE
DHS
DAO
DCM
DHSX
DARFUR
DAVID
DO
DEAX
DEFENSE
DEA
DTRO
DPRK
DARFR
DOC
DK
DTRA
DAC
DOD
DIEZ
DMINE
DRC
DCG
DPKO
DOT
DEPT
DOE
DS
DKEM
ECON
ETTC
EFIS
ETRD
EC
EMIN
EAGR
EAID
EFIN
EUN
ECIN
EG
EWWT
EINV
ENRG
ELAB
EPET
EIND
EN
EAIR
EUMEM
ECPS
ES
EI
ELTN
ET
EZ
EU
ER
EINT
ENGR
ECONOMIC
ENIV
EK
EFTA
ETRN
EMS
EPA
ESTH
ENRGMO
EET
EEB
EXIM
ECTRD
ELNT
ETRA
ENV
EAG
EREL
ENVIRONMENT
ECA
EAP
ECONOMY
EINDIR
EDUARDO
ETR
EUREM
ELECTIONS
ETRC
EICN
EXPORT
EMED
EARG
EGHG
EINF
ECIP
EID
ETRO
EAIDHO
EENV
EURM
EPEC
ERNG
ENERG
EIAD
EAGER
EXBS
ED
ELAM
EWT
ENGRD
ERIN
ECO
EDEV
ECE
ECPSN
ENGY
EL
EXIMOPIC
ETRDEC
ECCT
EINVECON
EUR
ENRGPARMOTRASENVKGHGPGOVECONTSPLEAID
EFI
ECOSOC
EXTERNAL
ESCAP
EITC
ETCC
EENG
ERA
ENRD
EBRD
ENVR
ETRAD
EPIN
ECONENRG
EDRC
ETMIN
ELTNSNAR
ECHEVARRIA
ELAP
EPIT
EDUC
ESA
EAIDXMXAXBXFFR
EETC
EIVN
EBEXP
ESTN
EGOV
ECOM
EAIDRW
ETRDEINVECINPGOVCS
ETRDGK
ENVI
ELN
EPRT
EPCS
EPTED
ERTD
EUM
EAIDS
ETRB
EFINECONEAIDUNGAGM
EDU
EV
EAIDAF
EDA
EINTECPS
EGAD
EPREL
EINVEFIN
ECLAC
EUCOM
ECCP
ELDIN
EIDN
EINVKSCA
ENNP
EFINECONCS
EFINTS
ETC
EAIRASECCASCID
EINN
ETRP
EFQ
ECOQKPKO
EGPHUM
EBUD
ECONEINVEFINPGOVIZ
ECPC
ECONOMICS
ENERGY
EIAR
EINDETRD
ECONEFIN
ECOWAS
EURN
ETRDEINVTINTCS
EFIM
ETIO
EATO
EIPR
EINVETC
ETTD
ETDR
EIQ
ECONCS
ENRGIZ
EAC
ESPINOSA
EAIG
ENTG
EUC
ERD
EINVECONSENVCSJA
EEPET
EUNCH
ESENV
ECINECONCS
ETRDECONWTOCS
ECUN
FR
FI
FOREIGN
FARM
FAO
FK
FCSC
FREEDOM
FARC
FAS
FJ
FIN
FINANCE
FAC
FBI
FTAA
FM
FCS
FAA
FETHI
FRB
FRANCISCO
FORCE
FTA
FT
FMGT
FCSCEG
FDA
FERNANDO
FINR
FIR
FDIC
FOR
FOI
FKLU
FO
FMLN
FISO
GM
GERARD
GT
GA
GG
GR
GTIP
GB
GH
GZ
GV
GE
GAZA
GY
GJ
GEORGE
GOI
GCC
GMUS
GI
GABY
GLOBAL
GUAM
GC
GOMEZ
GUTIERREZ
GL
GOV
GKGIC
GF
GU
GWI
GARCIA
GTMO
GANGS
GIPNC
GAERC
GREGG
GUILLERMO
GASPAR
HA
HYMPSK
HO
HK
HUMAN
HR
HU
HN
HHS
HIV
HURI
HDP
HUD
HUMRIT
HSWG
HUMANITARIAN
HIGHLIGHTS
HUM
HUMANR
HL
HILLARY
HSTC
HCOPIL
HADLEY
HOURANI
HARRIET
HESHAM
HI
HNCHR
HEBRON
HUMOR
IZ
IN
IAEA
IS
IMO
ILO
IR
IC
IT
ITU
ID
IV
IMF
IBRD
IWC
ICAO
INF
ICRC
IO
IPR
IRAQI
ISO
IK
ISRAELI
IDB
INFLUENZA
IRAQ
INL
IQ
ICES
IRMO
IRAN
ISCON
IGAD
ITALY
INTERNAL
ILC
ISSUES
ICCAT
IADB
ICTY
ICTR
ITPGOV
ITALIAN
IQNV
IRDB
INMARSAT
INCB
INRB
ICJ
ISRAEL
INR
IFO
ITRA
IEA
ISPA
IOM
ITRD
IL
IHO
IFAD
IPROP
IDLI
ISCA
INV
IBB
ISPL
INRA
INTELSAT
ISAF
IRS
IEF
ITER
ISAAC
ICC
INDO
IIP
IATTC
IND
INS
IZPREL
IAHRC
IEFIN
IACI
INNP
IA
INTERPOL
IFIN
IRAJ
IX
IF
ITPHUM
ITA
IP
IZEAID
IRPE
IDA
ISLAMISTS
ITF
INRO
IBET
IDP
IRC
KMDR
KPAO
KOMC
KNNP
KFLO
KDEM
KSUM
KIPR
KFLU
KE
KCRM
KJUS
KAWC
KZ
KSCA
KDRG
KCOR
KGHG
KPAL
KTIP
KMCA
KCRS
KPKO
KOLY
KRVC
KVPR
KG
KWBG
KTER
KS
KN
KSPR
KWMN
KV
KTFN
KFRD
KU
KSTC
KSTH
KISL
KGIC
KAPO
KSEP
KDP
KFIN
KTEX
KTIA
KUNR
KCMR
KCIP
KMOC
KTDB
KBIO
KMPI
KSAF
KFEM
KUNC
KPRV
KIRC
KACT
KRMS
KNPT
KMFO
KHIV
KHLS
KPWR
KCFE
KREC
KRIM
KHDP
KVIR
KNNNP
KCEM
KIRF
KGIT
KLIG
KNUP
KSAC
KNUC
KFRDCVISCMGTCASCKOCIASECPHUMSMIGEG
KTBT
KSCI
KIDE
KPGOV
KLPM
KTDD
KOCI
KNNC
KOMS
KBCT
KLFU
KLAB
KSEO
KICC
KJUST
KUWAIT
KSEC
KUK
KEDEM
KJRE
KMRS
KSRE
KREISLER
KSCS
KPIR
KPOA
KESS
KCOM
KWIR
KIVP
KRCM
KGLB
KPOW
KPOL
KSEAO
KNAP
KCUL
KPREL
KREF
KPRP
KICA
KPMI
KPRM
KQ
KPOP
KFSC
KPFO
KPALAOIS
KRM
KBWG
KCORR
KVRC
KR
KFTN
KTTB
KNAR
KINR
KWN
KCSY
KIIP
KPRO
KREL
KFPC
KW
KWM
KRFD
KFLOA
KMCC
KIND
KNEP
KHUM
KSKN
KT
KOMO
KDRL
KTFIN
KSOC
KPO
KGIV
KSTCPL
KSI
KNNB
KNDP
KICCPUR
KDMR
KFCE
KIMMITT
KMNP
KOMCSG
KGCC
KRAD
KCRP
KAUST
KWAWC
KCHG
KRDP
KPAS
KITA
KMSG
KTIAPARM
KPAOPREL
KWGB
KIRP
KMIG
KSEI
KLSO
KWNN
KHSA
KCRIM
KNPP
KPAONZ
KWWW
KGHA
KY
KCRCM
KGCN
KPLS
KPAOY
KRIF
KTRD
KTAO
KJU
KBTS
KWMNPHUMPRELKPAOZW
KO
KEMR
KENV
KEAI
KWAC
KFIU
KWIC
KNNO
KPAI
KTBD
KILS
KPA
KRCS
KWBGSY
KNPPIS
KNNPMNUC
KERG
KLTN
KLIP
KTLA
KAWK
KVRP
KAID
KX
KWCI
KNPR
KCFC
KNEI
KFTFN
KTFM
KCERS
KDEMAF
KMEPI
KEMS
KDRM
KBTR
KEDU
KIRL
KNNR
KMPT
KPDD
KPIN
KDEV
KAKA
KFRP
KINL
KWWMN
KWBC
KA
KOM
KWNM
KFRDKIRFCVISCMGTKOCIASECPHUMSMIGEG
KRGY
KNNF
KICR
KIFR
KWMNCS
KPAK
KDDG
KCGC
KID
KNSD
KMPF
KWMM
LY
LE
LABOR
LH
LN
LO
LAB
LT
LAURA
LTTE
LG
LU
LI
LA
LB
LOTT
LORAN
LAW
LVPR
LARREA
LEBIK
LS
LOVE
LR
LEON
LAVIN
LOG
MU
MARR
MX
MASS
MOPS
MNUC
MCAP
MTCRE
MRCRE
MTRE
MASC
MY
MK
MDC
MG
MO
MEPN
MW
MILI
MCC
MR
MEDIA
MZ
MEPP
MOPPS
MA
MAS
MI
MP
MIL
MV
MC
MD
MCA
MT
MARITIME
MOPSGRPARM
MAAR
MOROCCO
MCAPS
MOOPS
ML
MN
MEPI
MNUCPTEREZ
MTCR
MUNC
MPOS
MONUC
MAR
MGMT
MENDIETA
MARIA
MONTENEGRO
MURRAY
MOTO
MACP
MINUSTAH
MCCONNELL
MGT
MARQUEZ
MANUEL
MNUR
MF
MOHAMMAD
MAPP
MOHAMED
MNU
MFA
MTS
MLS
MIAH
MEETINGS
MERCOSUR
MED
MARAD
MNVC
MINURSO
MIK
MARK
MBM
MILITARY
MAPS
MILA
MACEDONIA
MICHEL
MASSMNUC
MUCN
MQADHAFI
MPS
MARRGH
NZ
NATO
NI
NO
NU
NG
NL
NPT
NS
NP
NA
NASA
NSF
NTTC
NAS
NEA
NANCY
NSG
NRR
NATIONAL
NKNNP
NMNUC
NSC
NC
NE
NR
NARC
NGO
NELSON
NATEU
NDP
NIH
NK
NIPP
NERG
NSSP
NSFO
NATSIOS
NFSO
NTDB
NT
NCD
NEGROPONTE
NATOIRAQ
NAR
NZUS
NCCC
NH
NAFTA
NEW
NRG
NUIN
NOVO
NATOPREL
NEY
NV
NICHOLAS
NPA
NW
NORAD
NPG
NOAA
OPRC
OPDC
OTRA
OECD
OVIP
OREP
ODC
OIIP
OAS
OSCE
OPIC
OMS
OIC
OFDA
OEXC
OFDP
OPCW
OCED
OIE
OSCI
OM
OPAD
ODIP
OPCD
OCII
ORUE
ODPC
OPPI
ORA
OCEA
OREG
OUALI
OMIG
ODAG
OPREP
OFFICIALS
OSAC
OEXP
OPEC
OFPD
OMAR
ORC
OAU
OPDP
OIL
OVIPPRELUNGANU
OSHA
OTRD
OPCR
OF
OFDPQIS
OSIC
OHUM
OTR
OBSP
OGAC
OTRAORP
OESC
OVP
ON
OES
OTAR
OCS
PREL
PGOV
PARM
PINR
PHUM
PM
PREF
PTER
PK
PINS
PBIO
PHSA
PE
PBTS
PA
PL
POL
PAK
POV
POLITICS
POLICY
PROP
PRELTBIOBA
PKO
PO
PIN
PNAT
PU
PHAM
PALESTINIAN
PTERPGOV
PGOVPREL
PKPA
PHYTRP
PP
PTEL
PREC
PENA
PRM
PELOSI
PAS
PRELAF
PRE
PUNE
PSOE
POLM
PRELKPAO
PIRF
PGPV
PARMP
PRELL
PVOV
PROV
POLUN
PS
PHUMPTER
PROG
PRELGOV
PERSONS
PERURENA
PKK
PRGOV
PH
POLITICAL
PLAB
PDEM
PCI
PRL
PREM
PINSO
PEREZ
PPAO
PERM
PETR
PERL
PBS
PGOVZI
PINT
PARMS
PCON
PETERS
PRELBR
PMIL
PSOCI
PF
PLO
PNUM
PTERM
PJUS
PNIR
PHUMKPAL
PG
PREZ
PGIC
PAO
PTBS
PROTECTION
PRELPK
PGOVENRG
PRELKPKO
PATTY
PSOC
PARTIES
PRELSP
PGOVEAIDUKNOSWGMHUCANLLHFRSPITNZ
PMIG
PAIGH
PARK
PETER
PPREL
PTERPREL
PHUS
PKPO
PGOVECON
POUS
PMAR
PWBG
PAR
PARMIR
PGOVGM
PHUH
PTE
PY
PPEL
PDOV
PGOVSOCI
PGOVPM
PRELEVU
PGOR
PRELKPAOIZ
PBTSRU
PGVO
PHUMR
PPD
PGV
PRAM
PINL
PSI
PKPAL
PPA
PTERE
PGOF
PINO
PREO
PHAS
PRHUM
PHUMA
PGO
PAC
PRESL
PORG
PKFK
PEPR
PRELP
PREFA
PNG
PFOR
PGOVLO
PHUMBA
PREK
PHUME
PHJM
POLINT
PGOVE
PHALANAGE
PARTY
PECON
PEACE
PROCESS
PLN
PEDRO
PASS
PCUL
PGGV
PSA
PGOVSMIGKCRMKWMNPHUMCVISKFRDCA
PGIV
PHUMPREL
PRFE
POGOV
PEL
PBT
PAMQ
PINF
PSEPC
POSTS
PAHO
PHUMPGOV
PGOC
PNR
RS
RP
RU
RW
RFE
RCMP
RIGHTSPOLMIL
REFORM
RO
REACTION
REPORT
ROW
ROBERT
REL
RIGHTS
RA
RELATIONS
REGION
RAFAEL
REGIONAL
RAY
ROBERTG
RPREL
RAMONTEIJELO
RM
RATIFICATION
RREL
RBI
RICE
ROOD
RODENAS
RUIZ
RELFREE
RODHAM
RGY
RUEHZO
RELIGIOUS
RODRIGUEZ
RUEUN
RELAM
RSP
RF
REO
ROSS
RENE
RUPREL
RI
REMON
RPEL
RSO
SCUL
SENV
SOCI
SZ
SNAR
SO
SP
SU
SY
SMIG
SYR
SA
SW
SG
SF
SR
SYRIA
SNARM
SPECIALIST
START
SNIG
SCI
SI
SGWI
SE
SIPDIS
SANC
SADC
SELAB
SN
SETTLEMENTS
SENVENV
SCIENCE
SENS
SPCE
SENC
SCOM
SPAS
SECURITY
SL
SOCIETY
SOSI
SENVEAGREAIDTBIOECONSOCIXR
SEN
SPECI
ST
SENVCASCEAIDID
SC
SECRETARY
STR
SNA
SOCIS
SEP
SK
SHUM
SYAI
SMIL
STEPHEN
SNRV
SKCA
SENSITIVE
SECI
SCUD
SCRM
SGNV
SECTOR
SAARC
SENVSXE
SASIAIN
SWMN
STEINBERG
SOPN
SOCR
SCRS
SILVASANDE
SWE
SARS
SNARIZ
SUDAN
SENVQGR
SNARKTFN
SAAD
SD
SAN
SIPRNET
SM
STATE
SFNV
SSA
SPCVIS
SOFA
SCULKPAOECONTU
SPTER
SKSAF
SENVKGHG
SHI
SEVN
SPSTATE
SMITH
SH
SNARCS
SNARN
SIPRS
TBIO
TW
TRGY
TSPA
TU
TPHY
TI
TX
TH
TIP
TC
TSPL
TNGD
TS
TZ
TP
TK
TURKEY
TERRORISM
TPSL
TINT
TRSY
TERFIN
TPP
TT
TF
TECHNOLOGY
TE
TAGS
TECH
TRAFFICKING
TN
TJ
TL
TO
TD
TREATY
TR
TA
TIO
THPY
TPSA
TRAD
TNDG
TVBIO
TWI
TV
TWL
TWRO
TAUSCHER
TRBY
TSPAM
TREL
TRT
TNAR
TFIN
TPHYPA
TWCH
THOMMA
THOMAS
TERROR
TRY
TBID
UK
UNESCO
UNSC
UNGA
UN
US
UZ
USEU
UG
UP
UNAUS
UNMIK
USTR
UY
UNSCD
USUN
UV
UNDC
UNRWA
UNPUOS
USAID
UNSCR
UNODC
UNHCR
UNRCR
UNDP
UNCRIME
UA
UNHRC
UNEP
UNBRO
UNCSD
UNO
UNCND
UNCHR
USTRUWR
USAU
UNICEF
UNCC
USPS
UNOMIG
UNESCOSCULPRELPHUMKPALCUIRXFVEKV
UNFICYP
UR
UNAMA
UNCITRAL
UNVIE
USTDA
USNC
USTRPS
USCC
UNEF
UNGAPL
UNSCE
USSC
UEU
UNMIC
UNTAC
USDA
UNCLASSIFIED
UNA
UNCTAD
UNMOVIC
USGS
UNFPA
UNSE
USOAS
USG
UE
UAE
UNWRA
UNION
UNCSW
UNCHS
UNDESCO
UNC
UB
UNSCS
UKXG
UNGACG
UNHR
USPTO
UNCHC
UNFCYP
UNIDROIT
WHTI
WIPO
WTRO
WHO
WI
WFP
WHA
WTO
WMO
WEET
WZ
WBG
WS
WE
WA
WEF
WAKI
WILLIAM
WHOA
WSIS
WCI
WCL
WMN
WEBZ
WW
WWBG
WMD
WWT
WWARD
WITH
WMDT
WTRQ
WCO
WALTER
WEU
WB
WBEG
Browse by classification
Community resources
courage is contagious
Viewing cable 07GUANGZHOU603, CSR in the Classroom and on the Factory Floor
If you are new to these pages, please read an introduction on the structure of a cable as well as how to discuss them with others. See also the FAQs
Understanding cables
Every cable message consists of three parts:
- The top box shows each cables unique reference number, when and by whom it originally was sent, and what its initial classification was.
- The middle box contains the header information that is associated with the cable. It includes information about the receiver(s) as well as a general subject.
- The bottom box presents the body of the cable. The opening can contain a more specific subject, references to other cables (browse by origin to find them) or additional comment. This is followed by the main contents of the cable: a summary, a collection of specific topics and a comment section.
Discussing cables
If you find meaningful or important information in a cable, please link directly to its unique reference number. Linking to a specific paragraph in the body of a cable is also possible by copying the appropriate link (to be found at theparagraph symbol). Please mark messages for social networking services like Twitter with the hash tags #cablegate and a hash containing the reference ID e.g. #07GUANGZHOU603.
Reference ID | Created | Released | Classification | Origin |
---|---|---|---|---|
07GUANGZHOU603 | 2007-05-24 09:09 | 2011-08-23 00:00 | UNCLASSIFIED//FOR OFFICIAL USE ONLY | Consulate Guangzhou |
VZCZCXRO5166
RR RUEHCN RUEHGH RUEHVC
DE RUEHGZ #0603/01 1440909
ZNR UUUUU ZZH
R 240909Z MAY 07
FM AMCONSUL GUANGZHOU
TO RUEHC/SECSTATE WASHDC 6088
INFO RUEHOO/CHINA POSTS COLLECTIVE
RUEAWJA/DOJ WASHDC
RUEHC/DEPT OF LABOR WASHDC
RUCPDOC/USDOC WASHDC
RUEAEPA/HQ EPA WASHDC
RUEAIIA/CIA WASHDC
RUEKJCS/DIA WASHDC
RHHMUNA/HQ USPACOM HONOLULU HI
UNCLAS SECTION 01 OF 02 GUANGZHOU 000603
SIPDIS
SENSITIVE
SIPDIS
USPACOM FOR FPA
E.O. 12958: N/A
TAGS: ELAB PHUM EINV CH
SUBJECT: CSR in the Classroom and on the Factory Floor
(U) This message is sensitive but unclassified. Please handle
accordingly.
¶1. (SBU) SUMMARY: Domestic factories are struggling to comply with
multiple responsibilities that can complement one another but that
may at times also be at variance with one another: their buyers'
corporate social responsibility (CSR) codes of conduct and with
government regulations on wages and work hours, according to
participants in a recent training seminar run by U.S. NGO Business
for Social Responsibility (BSR). A recent garment industry survey
revealed that 70 percent of China's garment factories maintain
fraudulent documents, 30 percent of the workers are paid below
minimum wage, and almost all workers work more hours than legally
permitted. Though factories can improve efficiency and increase
wages though CSR practices, the transition from noncompliance to
compliance is difficult and slow. END SUMMARY.
¶2. (SBU) During a visit by State DRL Program Officer Samuel Chang on
May 15-16, Econoff and Chang attended the closing session of a CSR
training program run by BSR, an organization that is funded in part
by DRL. The nine-month series of classes for factory managers
(mostly suppliers of multinational corporations) covered health and
safety management, labor regulations, and reducing overtime through
improved productivity. Chang and Econoff also visited a Hong
Kong-owned garment factory in Dongguan that supplies Sears and other
U.S. brands and that participated in the BSR training.
The Government Perspective
--------------------------
¶3. (SBU) Chinese officials are increasingly concerned with labor
compliance in factories and are less tolerant of violations,
according to the director of the Guangdong Labor and Social Security
Bureau's Labor Association and Information Center, Gan Wenchuan. In
addition, the new generation of migrant workers is less willing to
work for low wages and is more aware of legal rights. Surprisingly,
Gan was critical of the All-China Federation of Trade Unions
(ACFTU), which he said is supposed to protect the rights of workers
but instead protects the interests of enterprises. In response to a
question from factory managers, Gan said that the Chinese government
has shown no interest in raising the cap on overtime hours.
Factory Managers Discuss the Difficulties of Complying
--------------------------------------------- ---------
¶4. (SBU) Factory managers said they are audited between 5 and 15
times per year by their various buyers - a process that leads to
"audit fatigue." The buyers often have different and sometimes
conflicting codes of conduct regarding minimum wage and working
hours. The factory managers also noted the challenge of educating
senior management on CSR concepts and convincing them to make the
necessary investments - particularly in the garment industry, where
profit margins are tight. They also face greater scrutiny by the
Chinese media regarding labor practices. Nevertheless, the managers
highlighted their positive efforts, which include forming CSR
committees with worker representatives, increasing training hours,
and improving transparency. They noted that rotating workers
regularly and publishing worker handbooks has also improved
productivity.
Garment Industry Survey: Not a Pretty Picture
---------------------------------------------
¶5. (SBU) A survey of labor compliance in the garment industry
conducted by third-party firms hired by Sears revealed that the
state of compliance among China's garment factories is "dismal."
According to Sears Compliance Manager Johnny Wong, the survey found
that 70 percent of garment factories in China keep fraudulent sets
of documents in order to demonstrate compliance to buyers and
government officials. In addition, 30 percent of workers at garment
factories are paid below the minimum wage. The survey found that
garment workers average between 70 and 90 hours of work per week,
far above the legal limit of 49 hours (40 regular hours per week and
36 overtime hours per month). Overtime pay is typically not
calculated differently than regular pay (which is usually on a
piece-rate basis), and few factories pay all of the required social
insurance fees to the government. Factories also frequently do not
provide sufficient paid leave or use the required legal contracts,
according to the survey.
¶6. (SBU) According to Sears' Wong, China's garment factories would
not use false documents if buyers were willing to work with them to
GUANGZHOU 00000603 002 OF 002
improve labor compliance gradually. He said Sears' Wage Research
Improvement Program does this, but noted that progress has proven to
be difficult and slow. In a separate conversation, Sears Director
of Global Compliance Ian Spaulding said "many" of China's factories
do not comply with PRC wage laws, and "none" comply with working
hour laws. In part, this is because these laws do not reflect
market realities - for example, migrant workers themselves want to
work more than 49 hours per week to earn as much money as possible
in a short period of time.
Garment Factory: Getting Better, but Still Not There
--------------------------------------------- -------
¶7. (SBU) Greenway, a factory in Dongguan that produces women's
undergarments for Sears, Macy's, Nordstrums, and other U.S. brands,
is still not fully compliant with labor laws but has made
significant progress. According to the Hong Kong owners, until a
few years ago, they kept false records and routinely underpaid
workers. After working closely with Sears, and with training from
BSR, they have been able to reduce the wage gap and improve
productivity. Key to this is a new bonus system that provides
additional incentives for workers. Average wages have increased by
10 percent over the past year, turnover has reduced from 6 percent
to 3 percent, and the factory is not having trouble finding workers
(as is the case with many factories in the Pearl River Delta). The
factory also uses a UV light machine provided by the local police
department to check for fake identification cards used by minors.
¶8. (SBU) Despite these improvements, the factory managers estimated
that a few hundred of their approximately 5,000 workers do not
receive the minimum wage. The average wage in the factory is RMB
1,500 (USD 196); Dongguan's minimum wage, including overtime, is RMB
1,200 per month (USD 157). Workers also continue to work more hours
than legally permitted. The owners complained that their profits
have fallen considerably during the past 10 years because of pricing
pressure from buyers. Sears' Spaulding said he is encouraged by the
factory's adoption of CSR principles and its improving compliance
record, but highlighted the challenge of introducing change
country-wide. Sears alone has 2,800 suppliers in China.
¶9. (U) DRL Program Officer Samuel Chang did not have an opportunity
to review this cable.
GOLDBERG